Bromobutyl Rubber Stopper
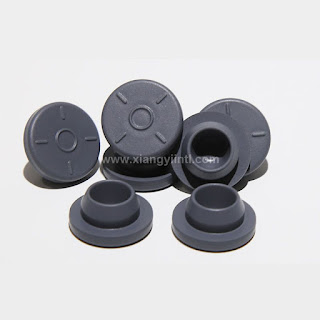
Bromobutyl Rubber Stopper Product Description bromobutyl rubber stopper Butyl rubber, derived synthetically from petrochemicals, is a copolymer of isobutylene, and to a smaller extent, isoprene. Subsequent halogenation results in a halobutyl rubber – typically bromobutyl or chlorobutyl. Advantage for Bromobutyl Rubber Stopper: 1. High cleanliness standard. Production under 100,000 class cleaning area, 2.Superior service system, with professional technical personnel, to provide customers with supporting and personalized services at any time; 3. Supply well-known pharmaceutical manufacturers home and abroad. Core material: Rubber from Exxon Mobil ● Advanced production system combines independent & cooperative research & development. ● Self inspection indicators ● 5 levels of 80-meter automatic cooling system. ● R&D system and central lab are according to international tech development direction and meet customers’ demand. ● 100 sets of advanced testing instruments and inspec